Trick Benefits and Considerations of Executing Plastic Extrusion in Your Projects
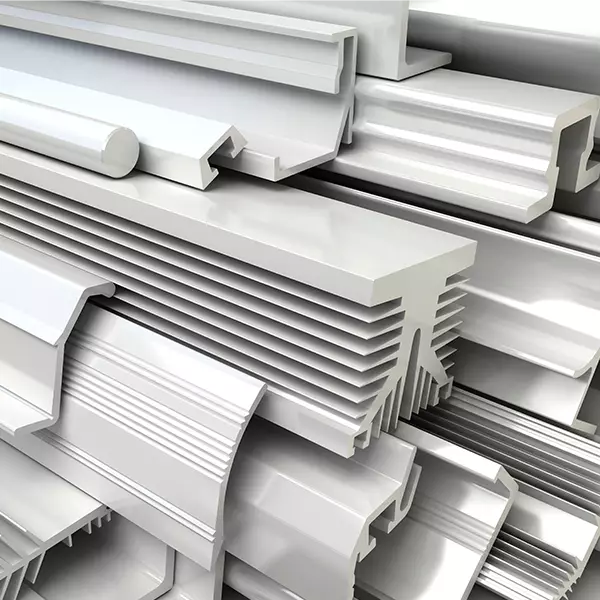
Recognizing the Essentials of Plastic Extrusion
Plastic extrusion, a staple in the manufacturing sector, is a procedure that includes melting raw plastic material and improving it right into a continuous account. This profile, when cooled down, can be cut right into preferred sizes or coiled for later usage. The elegance of plastic extrusion lies in its versatility. A variety of products, from piping to home window structures, can be created. The process requires an extruder, an intricate equipment with a warmed barrel, a turning screw, and a die at the end. The plastic product, in the form of pellets, is fed into the extruder, where it's thawed and forced via the die, taking its shape. The selection of plastic and the layout of the die identify the item's characteristics.

The Economic Benefit of Plastic Extrusion
The economic advantage of plastic extrusion lies primarily in two areas: cost-effective material production and beneficial production speeds. With plastic extrusion, businesses can generate high quantities of material at a reduced cost compared to various other techniques. The process flaunts an outstanding manufacturing rate, substantially decreasing time and additional enhancing its economic viability.
Cost-efficient Product Manufacturing
A substantial advantage of plastic extrusion is its amazing cost-effectiveness. This manufacturing procedure permits continuous, high-volume manufacturing with very little waste, which translates into lower expenses. The raw materials used, typically plastic pellets, are relatively low-cost contrasted to other compounds (plastic extrusion). The process itself needs less energy than several other manufacturing techniques, better decreasing prices. Additionally, the extrusion procedure permits a high level of precision in forming the plastic, lowering the demand for pricey post-production modifications or modifications. The longevity and long life of extruded plastic products typically imply less require for substitutes, contributing to long-lasting savings. All these elements make plastic extrusion a very cost-effective choice for lots of projects, supplying an eye-catching equilibrium in between price and performance.
Beneficial Production Speeds
While keeping the cost-effectiveness of the materials, one more noteworthy advantage of plastic extrusion lies in its fast production rates. This efficiency in the manufacturing process is credited to the constant nature of the extrusion procedure, permitting high-volume manufacturing in a fairly brief time span. The rate of production straight correlates to a reduction in labor prices and a rise in outcome, thereby enhancing the general economic viability of the procedure. The fast-paced production does not endanger the high quality of the final item, making certain reliable and consistent results. This mix of cost-effectiveness, speed, and quality emphasizes the substantial economic benefit of carrying out plastic extrusion in various tasks.
Convenience and Customization: The Toughness of Plastic Extrusion
One of the famous strengths of plastic extrusion depends on its flexibility and personalization potential. These top qualities open up the door to unlimited style possibilities, giving manufacturers the this website capability to tailor products to specific requirements. This enhanced degree of personalization not just boosts item performance but also significantly improves item originality.
Unlimited Style Possibilities
Plastic extrusion beams in its ability to supply virtually infinite design possibilities. This technique provides freedom to create complex shapes and complex accounts, a feat hard to achieve with other manufacture techniques. Owing to the liquid nature of liquified plastic, the process is versatile enough to produce a varied series of sizes, types, and dimensions. The plastic can be adjusted to match one-of-a-kind specifications, enabling the manufacturing of customized geometries and meeting specific client demands. Plastic extrusion can manage a variety of plastic types, increasing its application scope. This versatile technique, for that reason, serves a variety of industries from building to automotive, product packaging to electronics, and beyond. With plastic extrusion, the layout opportunities are basically countless.
Boosting Item Uniqueness
The flexibility of plastic extrusion can greatly improve product individuality. This process permits developers to experiment with different forms, dimensions, and colors, providing the flexibility to produce unique products that stand apart in the market. It is this modification that provides a distinct identification per item, distinguishing it Get the facts from its competitors.
In enhancement to its visual benefits, the customizability of plastic extrusion likewise uses useful advantages. Thus, plastic extrusion not only increases item individuality however also its energy and marketability.
Layout Limitations in Plastic Extrusion: What You Required to Know
Just how can make constraints potentially affect the procedure of plastic extrusion? While plastic extrusion is functional, design restrictions can curtail its benefits. Specific complicated styles may not be practical due to the constraints of the extrusion procedure, potentially limiting the development of intricate profiles. The process is much less suitable for hollow or multi-chambered structures. Furthermore, the extrusion procedure might not always offer the desired surface finish, especially for those needing high gloss or optical clearness. Product option can likewise posture difficulties, as not all polymers are appropriate for extrusion. High-temperature immune plastics, as an example, may offer problems. Recognizing these constraints is essential for efficient implementation of plastic extrusion in your projects. plastic extrusion.
Assessing the Environmental Impact of Plastic Extrusion
While understanding design limitations is a significant facet of plastic extrusion, it is similarly crucial to consider its ecological effects. The process of plastic extrusion entails melting plastic materials, possibly releasing harmful gases right into the environment. Utilizing recycled plastic products in the extrusion procedure can reduce environmental influence.
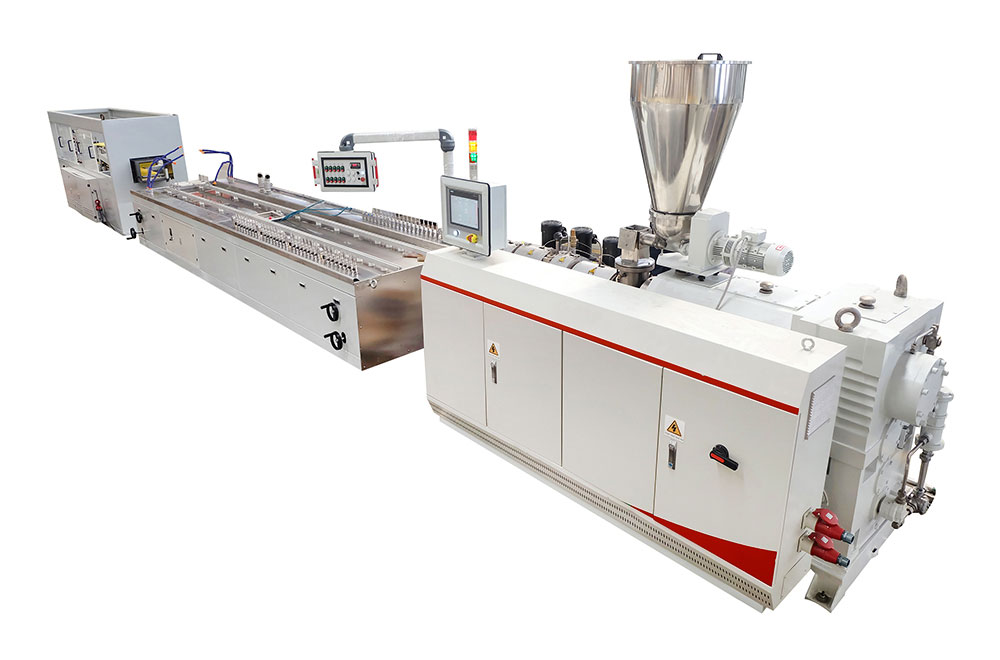
Study: Effective Projects Using Plastic Extrusion
Success stories in the area of plastic extrusion abound, demonstrating both the adaptability and efficiency of this production process. One significant instance is the development of PVC pipelines made use of in modern-day pipes. This process entails melting plastic and creating it into a continual tube, supplying considerable expense and longevity advantages. One more effective situation is the production of plastic film for packaging and farming. Via extrusion, makers can create highly personalized, slim, and durable films. Automotive industries also profit, using extruded plastic for components like trim or seals, improving car long life. These circumstances illustrate plastic extrusion's essential role in numerous sectors, vouching for its versatility, cost-effectiveness, and trusted outcome.
Conclusion
In conclusion, plastic extrusion offers a affordable and reliable method for generating intricate shapes with minimal waste. While it offers numerous benefits such as cost-effectiveness and flexibility, it's vital to consider prospective design constraints and environmental results. Applying recycled or biodegradable products can reduce these problems, boosting sustainability. Including plastic extrusion into jobs can cause successful end results, as confirmed by many case studies.
Plastic extrusion, a staple in the manufacturing industry, is a process that includes melting raw plastic product and reshaping it into a original site constant profile. Plastic extrusion can deal with a variety of plastic kinds, increasing its application range.Just how can design limitations possibly impact the process of plastic extrusion? The process of plastic extrusion includes melting plastic products, possibly releasing unsafe gases into the setting. Utilizing recycled plastic products in the extrusion process can lower environmental effect.